Constructing dams and retaining walls is more than just pouring concrete—it's a delicate balancing act between precision, pressure, and performance. These structures aren't merely utilitarian; they hold back the raw force of nature and protect infrastructure, ecosystems, and communities. From mountainous terrains to urban flood zones, building a reliable barrier means confronting logistical nightmares—remote access, tight timelines, and ever-present environmental concerns.
This is where concrete trailer pumps step in—not as an accessory, but as a game-changer. With their compact frames, long-distance pumping capacities, and unparalleled adaptability, concrete trailer pumps have quietly revolutionized large-scale civil engineering. They don't just pour concrete; they deliver it with grace, speed, and accuracy that traditional methods can rarely match.
The Practical Demands of Dam and Retaining Wall Construction
Access Constraints and Vertical Challenges
Remote project sites are notoriously difficult to reach, with narrow service roads and steep gradients complicating the transport of heavy machinery. Concrete trailer pumps offer a unique solution by separating the mixing process from the pumping phase. Instead of relocating an entire batch plant or depending on gravity-fed buckets, engineers can position trailer pumps at optimal vantage points—even on uneven terrain or alongside riversides.

Thanks to their high-pressure piston systems, these machines can pump concrete vertically up to 200 meters or more, which is crucial for dam faces and tall retaining walls. Reaching complex formwork from ground level without compromising flow quality isn't just convenient—it's essential for structural integrity.
Minimized Downtime, Maximized Output
On these critical projects, every delay ripples downstream—literally and figuratively. A stalled pour means risking cold joints or uneven curing, both of which can lead to catastrophic failures. Trailer-mounted pumps mitigate such risks by maintaining a consistent flow rate and minimizing interruptions.
Their hydraulic systems are designed for continuous duty cycles, and many come equipped with smart controls that monitor pressure, stroke length, and volume output. That means operators can detect clogs or inefficiencies early—and adjust on the fly. Less downtime equals tighter schedules, lower labor costs, and safer builds.
The Technical Edge: Precision, Reach, and Versatility
Fine-Tuned Flow Control for Structural Precision
In the realm of dams and walls, precision pouring is everything. Overfilling, underfilling, or over-vibrating concrete can compromise compaction and durability. Modern mobile concrete pumps offer variable displacement systems and digital pressure regulation, allowing operators to dial in the exact mix output needed for each lift.
Such fine-tuned control also ensures minimal rebound and segregation—a must when working with high-strength concrete blends or additives like fly ash and micro silica. Precision isn't a luxury in these builds—it's a structural necessity.
Multi-Zone Pouring with One Pump Station
Dams and retaining walls often stretch over long distances, with multiple lift points and staging zones. Instead of relocating equipment repeatedly, one trailer pump—connected with a well-designed pipeline system—can serve multiple sections of a project. This distributed reach not only saves time but reduces mechanical wear and unnecessary fuel consumption.
Additionally, many trailer pumps are equipped with remote controls, so operators can trigger pours from hundreds of feet away. In areas with active water flow or limited manpower, this autonomy makes all the difference.
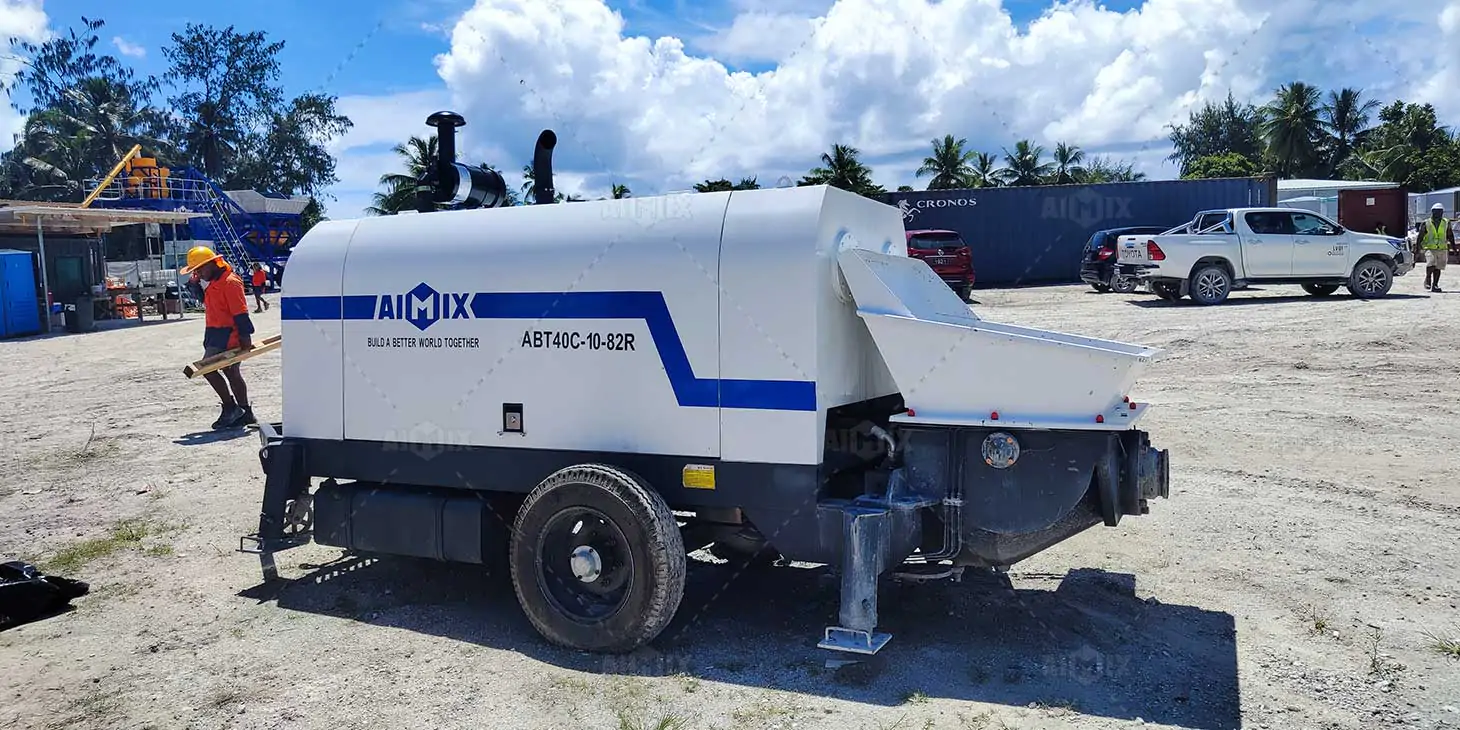
Environmental and Economic Benefits for Long-Term Sustainability
Lower Carbon Footprint and Reduced Site Disruption
Compared to crane-and-bucket methods or bulk mixers, trailer pumps offer a far greener footprint. They use less fuel, produce fewer emissions, and disturb the site less—especially important in ecologically sensitive areas. For dam projects near protected waterways or urban development zones, this matters immensely.
The smaller staging footprint also means reduced dust, noise, and vehicular traffic—making the working environment more harmonious for crews and communities alike. Sustainability isn't just about the materials used—it's about the machinery behind them.
Improved Cost Control and Return on Equipment Investment
Every contractor knows that labor inefficiencies and idle equipment chew through profits. Static concrete pumps strike a rare balance—they're affordable to acquire, inexpensive to run, and versatile across project types. From retaining walls on hillside homes to mega-scale hydroelectric dams, the same core technology applies.
Moreover, the long service life and minimal maintenance of trailer pumps make them a favorite among rental fleets and ownership models alike. When well-operated, they don't just pay for themselves—they become a profit center.
Conclusion
Dams and retaining walls demand more than brute strength—they demand finesse, consistency, and smart logistics. Concrete trailer pumps deliver all three, reshaping how the industry tackles these monumental builds. Whether perched on a cliffside or nestled in a valley, these machines bring power to precision, speed to complexity, and heart to concrete.